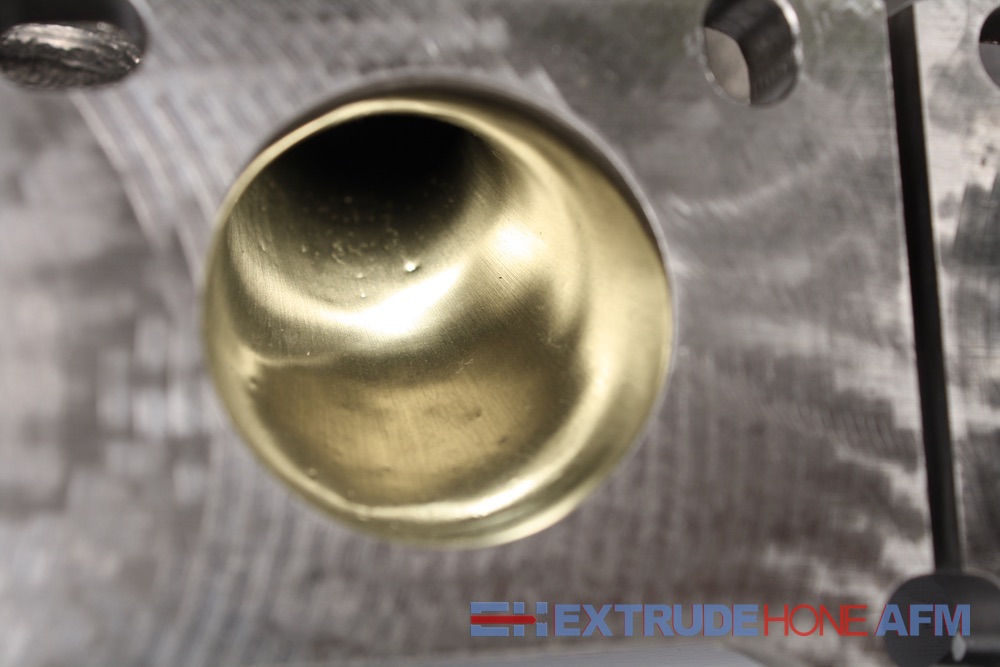
Precision is everything when it comes to manufacturing and machining, especially for industries that rely on smooth and efficient performance from their components. Internal surfaces, often overlooked, play a critical role in ensuring the overall functionality and longevity of parts. For companies seeking expert internal polishing in Nashville, TN, Extrude Hone AFM offers cutting-edge solutions that are tailored to meet your specific needs.
Whether your industry involves automotive components, medical devices, or aerospace parts, internal polishing ensures that every element works at its best. Let’s explore why internal polishing is essential, how it works, and why Extrude Hone AFM is the leading choice for internal polishing services in Nashville.
The Importance of Internal Polishing in Nashville, TN
Internal polishing is more than just an aesthetic enhancement—it’s about performance. Internal surfaces often experience friction, fluid flow, and interaction with other parts, making their smoothness and precision vital to the overall function of the product. Internal polishing eliminates rough surfaces, burrs, and imperfections that can lead to inefficiency, damage, or failure over time.
Our internal polishing in Nashville, TN caters to a wide variety of industries. Whether you’re manufacturing complex fuel systems, delicate medical devices, or precision aerospace parts, internal polishing ensures that your products meet the highest performance standards.
Why Internal Polishing Matters
- Improved Efficiency and Performance
Polished internal surfaces are critical in systems that rely on fluid dynamics, such as automotive fuel injectors or hydraulic systems. By smoothing out the interior of components, polishing minimizes flow resistance and ensures that the system operates at optimal efficiency. For industries like aerospace, where even the smallest inefficiencies can have a large impact, this step is non-negotiable.
- Reducing Wear and Tear
Friction is the enemy of longevity. Internal polishing reduces friction between moving parts, which helps to extend the life of a component. Rough internal surfaces can cause parts to wear down faster, leading to increased maintenance costs and reduced reliability. By polishing these surfaces, you’re helping your machinery last longer and perform more reliably over time.
- Burr Removal for Safety and Reliability
During the manufacturing process, small burrs or imperfections may form on the internal surfaces of parts. These imperfections can lead to blockages, reduced flow, or even mechanical failure. For industries like medical devices, where precision is absolutely essential, the presence of burrs can be disastrous. Internal polishing removes these imperfections, ensuring that components operate smoothly and consistently.
- Aesthetic and Functional Quality
While the primary reason for internal polishing is to improve function, it also enhances the overall quality of your product. Clean, polished surfaces reflect the attention to detail and high manufacturing standards that clients expect, whether in the automotive, medical, or industrial sectors.
How Internal Polishing Works
At Extrude Hone AFM, we use advanced techniques and state-of-the-art equipment to achieve flawless results in our internal polishing services. Our internal polishing in Nashville, TN, is customized to meet the unique needs of your project, regardless of industry.
- Abrasive Flow Machining (AFM): This technique uses an abrasive-laden polymer that is forced through the part, polishing its interior to the desired smoothness. AFM is ideal for parts with complex internal passages or areas that are difficult to reach with traditional methods.
- Electrochemical Machining (ECM): This non-contact process uses electrical current and a chemical electrolyte to remove material from the surface, polishing it without mechanical stress or heat. ECM is perfect for precision components that require burr removal and a smooth finish without the risk of damaging the part.
- Hydroerosive Grinding (HEG): HEG uses high-pressure fluid and abrasive material to refine internal surfaces, making it ideal for improving flow dynamics in parts such as nozzles and fuel injectors.
By offering a range of polishing techniques, we ensure that your parts receive the treatment they need for optimal performance and durability.
Applications of Internal Polishing
Internal polishing plays a vital role in a range of industries. Here are some common applications of our internal polishing in Nashville, TN:
- Automotive: Polishing fuel injectors, exhaust components, and engine parts to enhance performance, efficiency, and emissions control.
- Medical Devices: Ensuring smooth internal surfaces in medical instruments and implants for safety, reliability, and precision.
- Aerospace: Refining internal passages in aerospace components, where smooth airflow and minimal friction are essential for performance and safety.
- Energy and Power Generation: Polishing turbines, valves, and pipelines to improve flow dynamics and reduce wear in high-stress environments.
No matter your industry, internal polishing is a crucial step in ensuring that your products meet the highest standards of quality, safety, and performance.
Partner with Extrude Hone AFM for Internal Polishing in Nashville, TN
At Extrude Hone AFM, we understand the importance of precision and quality. Our internal polishing services are designed to provide you with the smoothest, most efficient components possible. By partnering with us, you’ll receive expert guidance, industry-leading polishing techniques, and a commitment to excellence in every project we undertake.
If you’re ready to improve the performance and reliability of your components with internal polishing in Nashville, TN, contact Extrude Hone AFM today at (562) 531-2976. Let us help you achieve the precision you need for long-lasting, high-performing products.